Nippon Sharyo Tilting System
@The high performance tilting system developed by Nippon Sharyo utilizing stroke difference of the air spring enables to realize safe and stable running
service in the curvilinear sections with high speed.
It provides an excellent ride comfort all the passengers including standees.
Outline of the Tilting System
@This system is featured as an air suspension tilting system which is utilizing special Leveling Valve and
Booster for rolling stocks.
- Major components
- A@Leveling Valve with Height Changer (hereafter, HCLV)
- B@Tilting Control Unit
- C@Booster
- The tilting angle of the carbody is 2 degrees.
Configuration of the tilting system is shown as Fig. 1
- @@@@@@
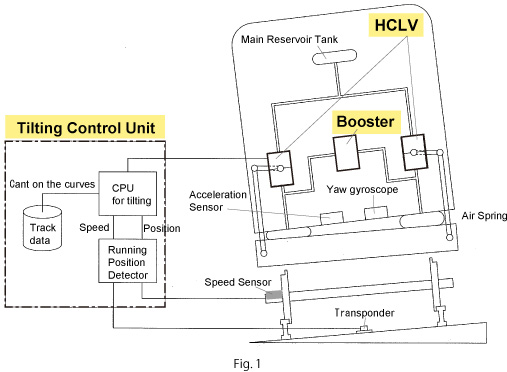
Role of each equipment
`@Leveling Valve with Height Changer (HCLV)
- HCLV is keeping the air suspension height at aimed level by intake and exhaust switching. The body is maintained at predetermined tilting angle.
-
While car is passing the curve, the system works to control as the level of outer side air spring would be higher and the level of inside air spring would be lower as the predetermined height level.
This control makes the length of LV rod expand and contract seemingly.
Once the offset of the air spring is over, each HCLV keep neutral position like normal LV. (figure 2)
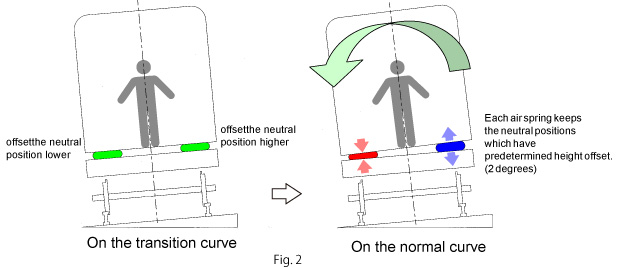
a@Tilting Control Unit
- Tilting Control Unit integrates the signal from speed sensor and figure out the current running position. Difference of distance arisen from wheel slip or skid is corrected
due to the information of ground transponder on ground or by the information of yaw gyroscope on vehicle. (The function of detecting running position)
- The current data calculated by the function of detecting running position plus pre–installed track data@are put together to decide the adequate tilt timing and give the command to activate HCLV. (The function of commanding tilt timing)
C Booster
- Booster is an equipment which mandatory transfers air from the inside air spring to the outer side air spring while running on the curves. By this equipment, tilting speed can be increased and air consumption is mitigated as well.
Tilting Mechanism
@Pattern diagram of tilt motion timing on a transition curve and normal curve is shown in Fig.3

Back up features
The tilting system is equipped with back up functions as follows.
Device |
Malfunction mode |
Back up method |
Tilting control unit |
Tilting command CPU down |
Command from next car |
Running position detector |
Position detector down |
Tail end car detector will make commands according to speed sensor and gyroscope |
Information transmission system |
Positioning information down |
Switch to exclusive back up line |
HCLV(Leveling Valve with Height Changer) |
command receipt failure |
HCLV act as normal LV
and tilting command is sent to dedicated back up LV which has predetermined tilt angle
|
EMU with tilting system for TRA (Taiwan Railways Administration)
@The EMU for TRA (Taiwan Railways Administration) is equipped with high performance tilting system developed by Nippon Sharyo. This EMU is
operated as a limited express train which is able to
serve safe and stable running over the curves with high speed. The maximum operating speed
is 140 km/h.
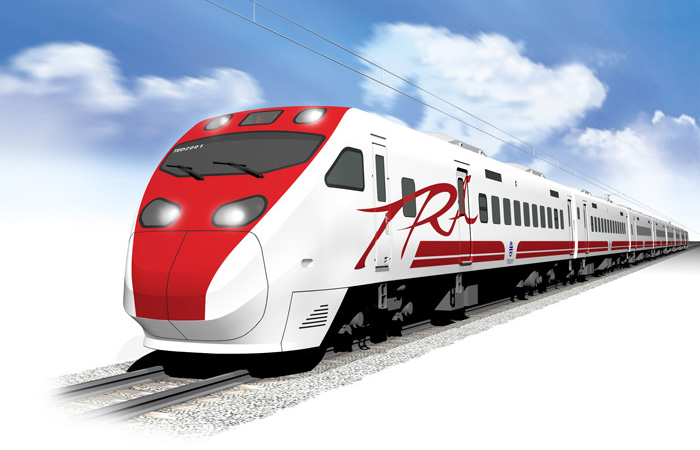
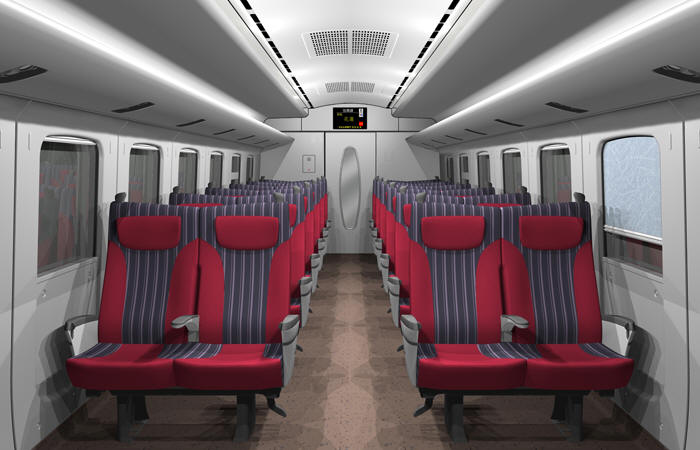