未来をつくる
自分から発信できる風通しのいい社風の中、
活躍の場が広がっています。
MEMBER
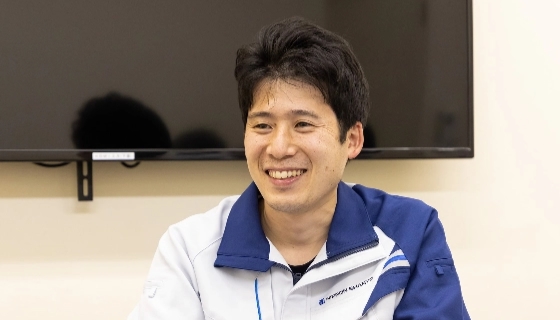
技術開発部
材料グループ(開発)
2011年入社
山﨑高生
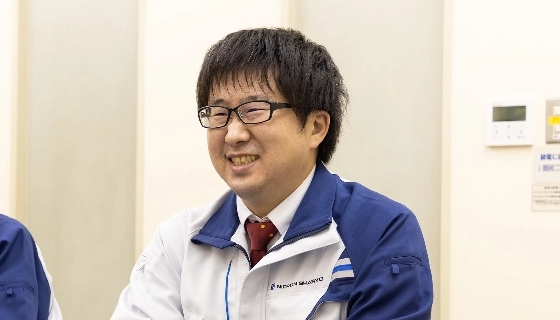
エンジニアリング本部
工事部 計画グループ(工事施工管理)
2012年入社
安川翔一
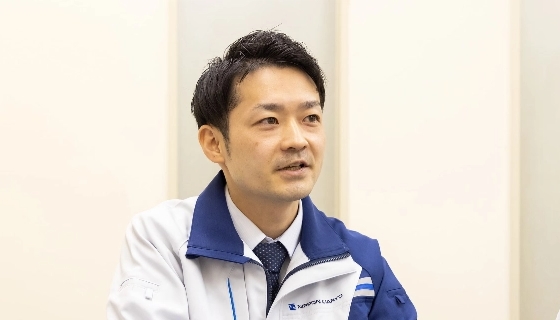
鉄道車両本部
管理部 人事総務グループ(企画)
2013年入社
石川雄一
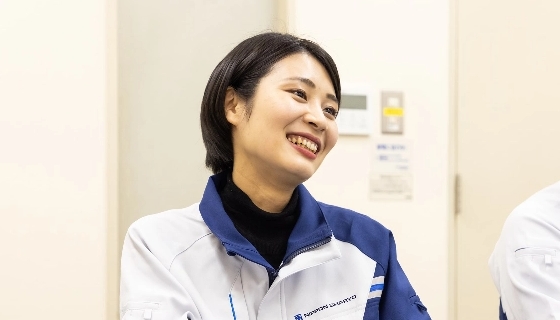
建設機械本部
資材部(調達)
2013年入社
鰐部沙紀
※所属・組織名は取材当時のものです
経験値と視野を広げる日本車両でのキャリアアップ
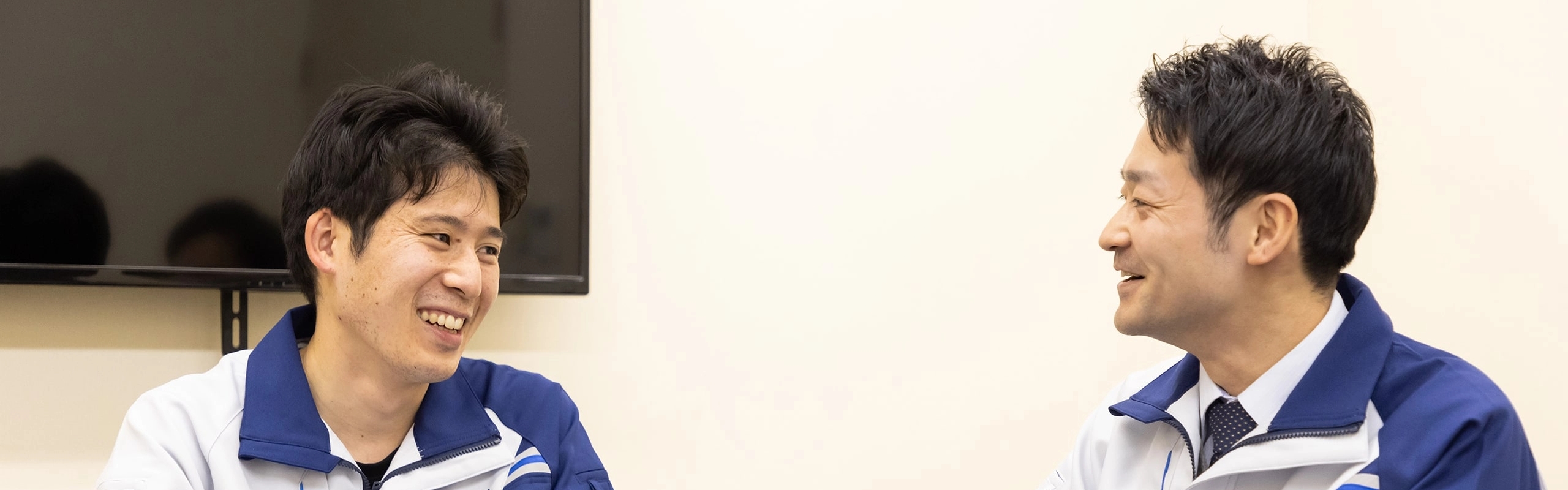
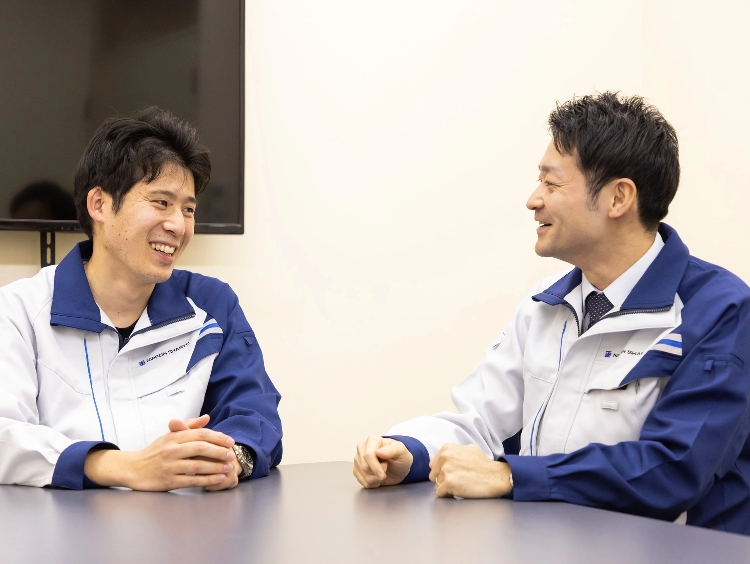
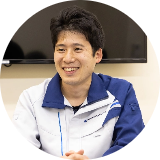
山﨑
現在、技術開発部の材料グループに所属していますが、入社後は鉄道車両の設計をしていました。設計を8年ほど経験して、今は材料関係の調査や調達、技術開発などを担当しています。もともと大学の専攻が近いという理由で材料に関わりたいと思っていました。設計に関わるうちにさまざまな課題が見えてきて、それを解決するために適した部署は材料グループだと思い、それを上司に伝え続けたところ、思いを活かせる部署に異動となりました。
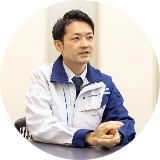
石川
鉄道車両本部の製作所内で1年間勤務した後、5年間、海外営業として主にインドネシアの地下鉄の受注後から納入までに関わりました。その後、現在所属する管理部に異動になり、本部全体の年度計画の策定、受注や設備投資に関する社内審査といった管理統括業務に携わった後、現在は人事総務に関する業務を行っています。
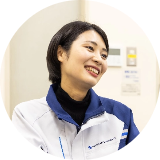
鰐部
入社後は、本社人事部の採用・教育チームで6年間、会社説明会運営などの採用業務や、新入社員研修をはじめとした階層別・選抜研修運営などの教育業務に携わっていました。全事業部と広く関わり日本車両の全体を見られる仕事を経て、入社当初から希望していたものづくりに近い部門である資材部への異動が叶い、現在は建設機械本部の資材部に所属しています。主に、建設機械の部品の納期・品質・価格の管理を行っています。
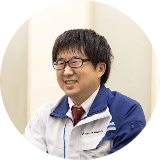
安川
入社以来、さまざまな現場を経験して、製品の据え付けなどの工事の管理スキルを身につけてきました。入社1年目は、エンジニアリング本部にて車両検修設備の現場据え付けを担当。2〜3年目はJR東海に出向して、リニア中央新幹線の車両の試験運用や保全などに関わり、全体的なシステムを学びました。それから当社のエンジニアリング本部が組織改変し、工事部という新しい部署が設けられ、その際に出向から戻り、再び車両研修設備の据え付けやメンテナンス、リニアの試験機の現場据え付け、試験にも携わりました。また異動により1年半ほど輸機・インフラ本部で橋梁架設の現場管理者としての経験を積み、現在のエンジニアリング本部での仕事に生かしています。
自分たちが感じる日本車両の強み
−最高品質を裏付ける、
技術力の高さとチームワーク−
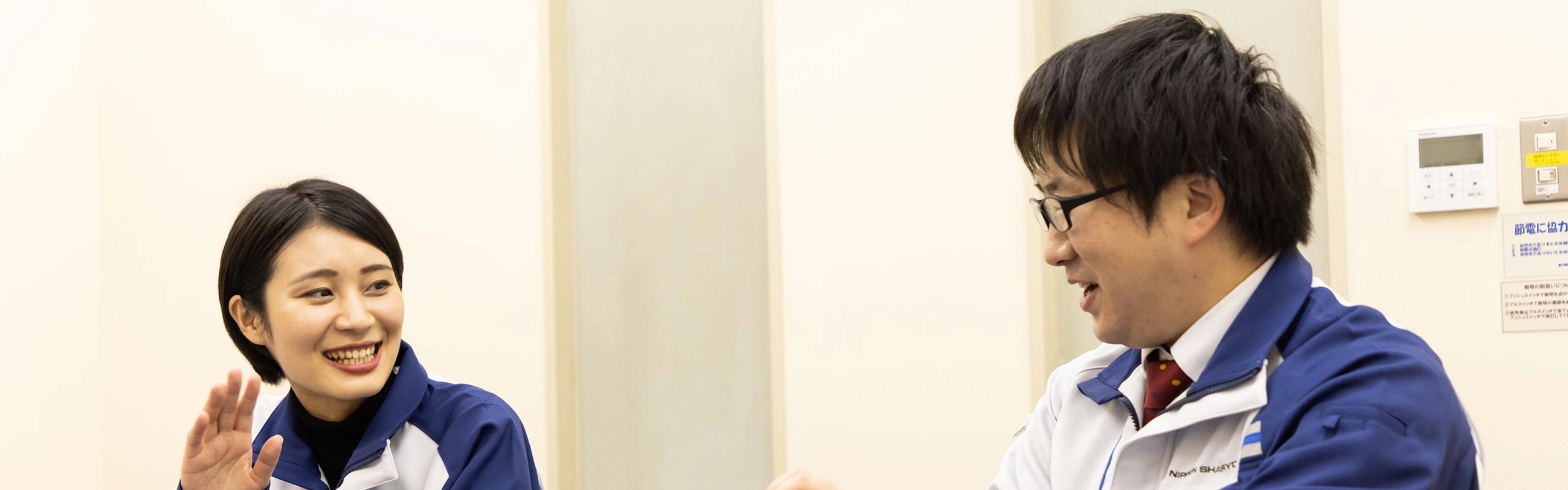
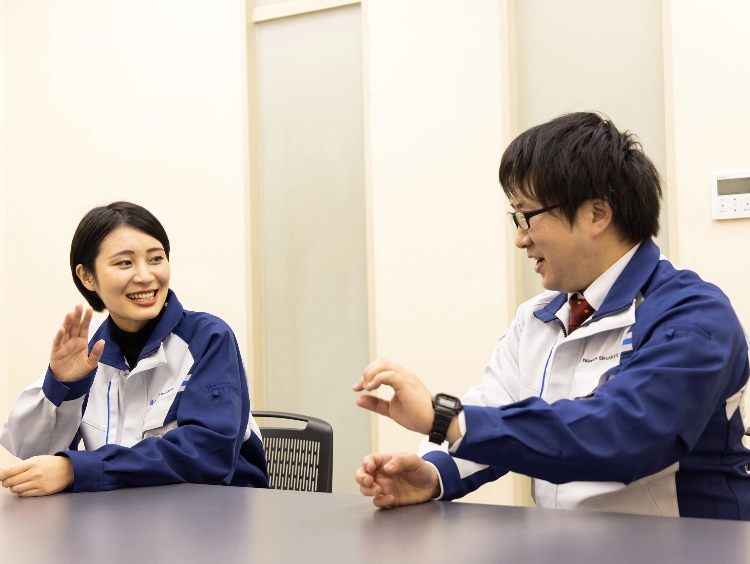
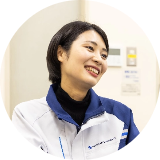
鰐部
事務系、技術系いずれの社員もみんな誠実さ、真面目さを感じます。「いいものを作りたい」「そのために自分ができることは何か」と前向きに考え、一生懸命に仕事をする人が多く、それが良いものづくりに繋がっていると思います。例えば、昨今は世界中で資材調達が難しくなっていますが、資材部だけでは解決が難しい問題に対して、どうすれば良いのかを各部署の方々が一緒に考えてくれるんです。簡単にあきらめたり特定の部署を責めたりするのではなく、みんなで何とかできないかと動く姿勢が心強くて、「本部全体で、良いものをつくろう」という強い気持ちが根っこにあるからこそのチームワークだと思います。
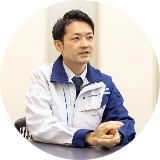
石川
チームワークや一体感は鉄道車両本部にもあると思います。JR東海の新型通勤車両315系の製作では、コンカレントエンジニアリングという手法を採用しました。設計段階から、資材部や製造部、品質保証部といった下流工程に設計情報を開示し、関係部門の意見を取り入れることにより、従前に比べて製作性が良く、非常に高い品質の車両を製作することができました。最高品質を目指し、一丸となってものづくりに取り組むという日本車両の強みが現れた事例だと思います。
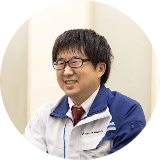
安川
私たちはJR東海のグループ会社ですので、鉄道車両や周辺の機械設備も含めて、JR東海との共同開発によって、さらに技術を高められるのも強みだと思います。技術だけでなく、出向などの人材交流によって得られる知識も多いです。私はJR東海に出向し、車両を製造する立場から、それらを運用する立場になりました。その経験を活かし、メーカーとしての視点だけでなく、運用側の視点からお客様が本当に求める品質を考え、提案・提言するようにしています。
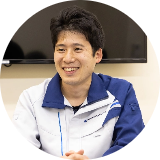
山﨑
各本部で得意不得意がありますから、時折、別の事業所から「他部署ではこんな時どうしていますか」と聞かれることもあります。こうした技術交流も品質向上に繋がっていると思います。社内にはいろんなプロがいますから。
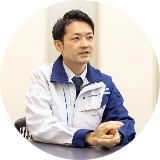
石川
当社は現場の技術力も高いと考えています。鉄道車両は金属からなる製品ですので、その製造にあたっては、溶接の技術力が品質に直接関係してきます。毎年、アルミの溶接技術を競う全国大会がありますが、鉄道車両本部は、過去9回の優勝を含む、計33回の入賞実績*を誇っています。*2022年4月時点データ
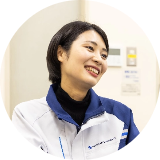
鰐部
現場の技術力が高いだけに、技能伝承がこれからの目標になりますね。
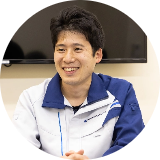
山﨑
現場から設計への意見があることも多いですよね。私が若手の頃は「本当にこれでいいと思っているのか」と指摘されたことが何度もあります。お客様に良いものを届けようという思いがあり、またこうして部門を超えて、直接、顔を付き合わせて本音で言い合えるのはいい関係だと思います。
生産性を高めるためのDX化やカーボンニュートラルへの考え
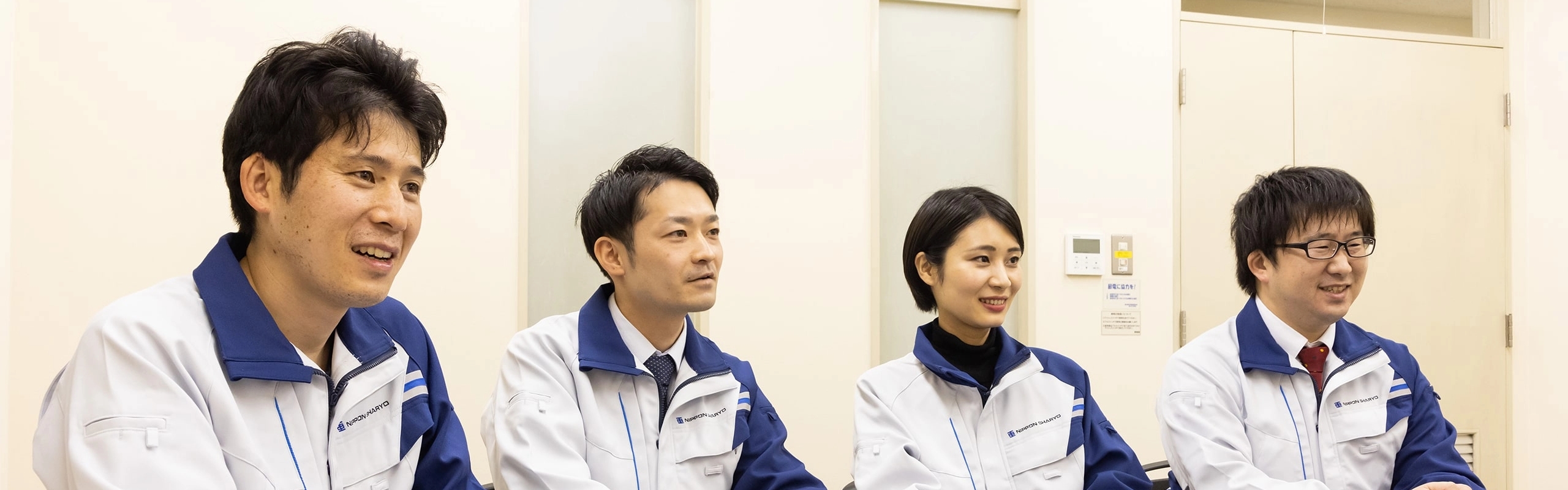
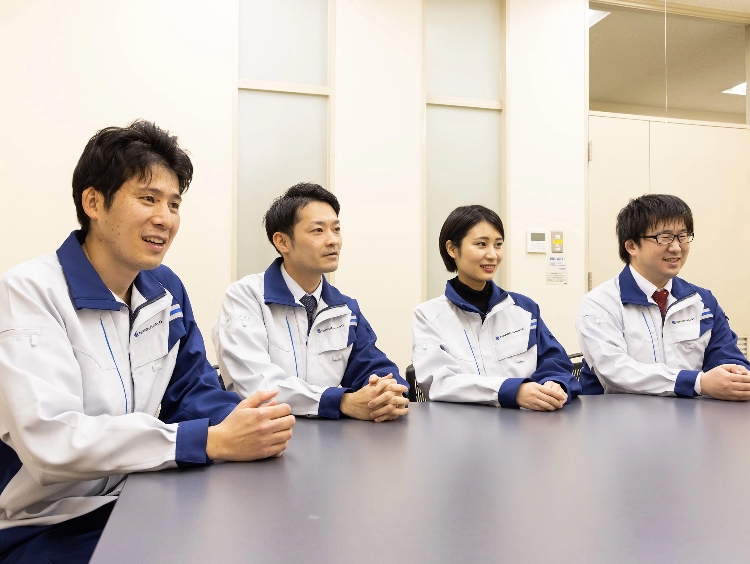
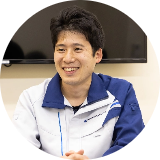
山﨑
技術的に挑戦していく分野だと思いますが、私個人の考えとしては、先ほども話題になった「技術伝承」に対して、デジタル活用できたらいいなと思います。最近では熟練工の技術をデータ化するツールも開発されています。優れた技術は私たちの財産ですので、アナログとデジタルを上手に融合させて若い技術者を育てて行きたいです。 またカーボンニュートラルに対しては、各事業部の考えが技術開発部に集まってきています。溶接のガスを変更するなど具体的な策がありますが、突き詰めると「無駄をどうなくすか」ということになると思います。現在、私が材料調査に関わる上で、環境に優しい素材を使っても、それにより製品寿命が短くなったり、不具合を起こして作り直しになったりすればかえって環境負荷を起こします。目に見える数字だけに囚われず、ものづくり企業として、質の高いものづくりの中で、いかにして無理無駄をなくし、生産性を高めることか考えることが大切だと思います。
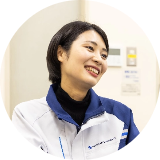
鰐部
私もその意見に同意です。建設機械本部では、生産性・信頼性を向上させるために、3Dデータをあらゆる工程で活用する取り組みを進めています。DX化することが目的なのではなく、それはあくまで手段であり、考え方のひとつです。DX化が有効なところでは積極的に活用していき、よりよいものづくりに繋げていきたいです。
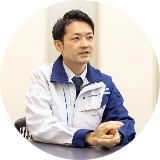
石川
鉄道車両本部ではまさにムダやムラをなくすという目的でDX化を進めています。設計段階では、先ほど紹介させていただいたコンカレントエンジニアリングのほか、3D設計の導入により事前検討の精度向上を図り、生産の効率化につなげる取り組みをしています。一方、生産段階では、図面や技術情報の電子化やタブレットなどのITツールの導入などによる、次世代的で効率的な製造現場づくりを推進しています。
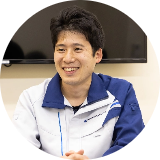
山﨑
数年前まで鉄道車両本部にいましたが、当時は紙の図面だったんですが、今は現場の人たちがタブレットで図面を確認している様子を見て、ずいぶん変わったなと思いました。
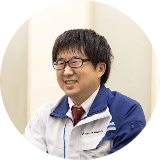
安川
工事現場は水道や電気がなく、発電機を置くことからスタートします。当然ネット環境もありませんからDX化という視点は少なく、逆に無駄を省くという視点には従来から重きを置かれています。早くから3D設計を活用して製造の手戻りをなくし、資材などの無駄をなくす。それが利益を上げることにも繋がります。しかし、一方で安心安全のために投資をする必要もあります。この見極めが大切ですね。
明日の日本車両を支える若手のみなさん
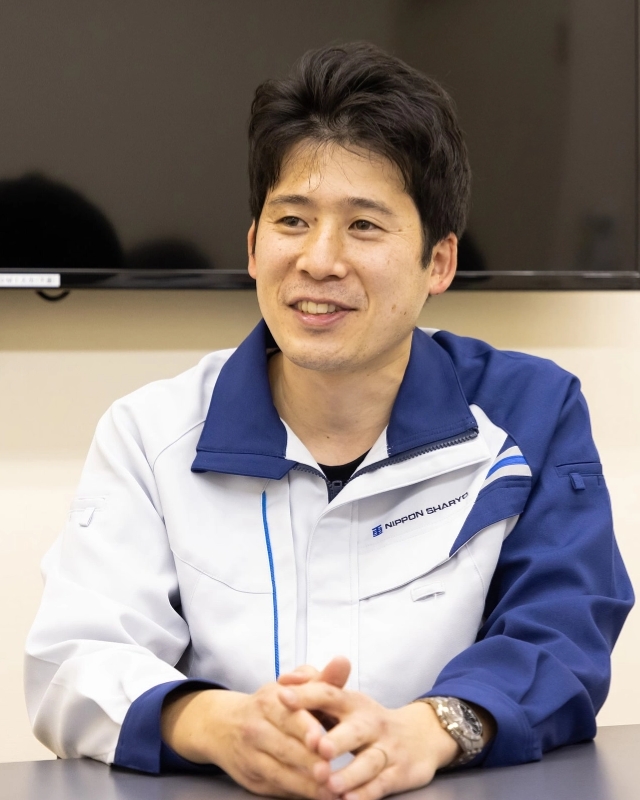
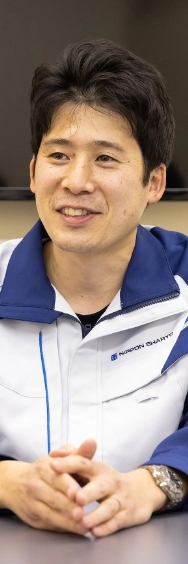
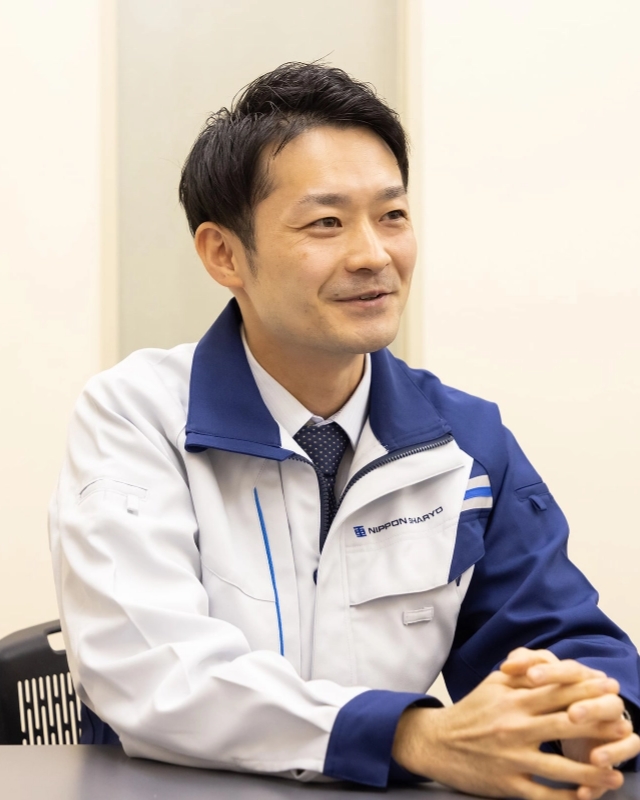
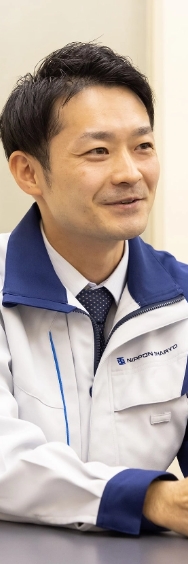
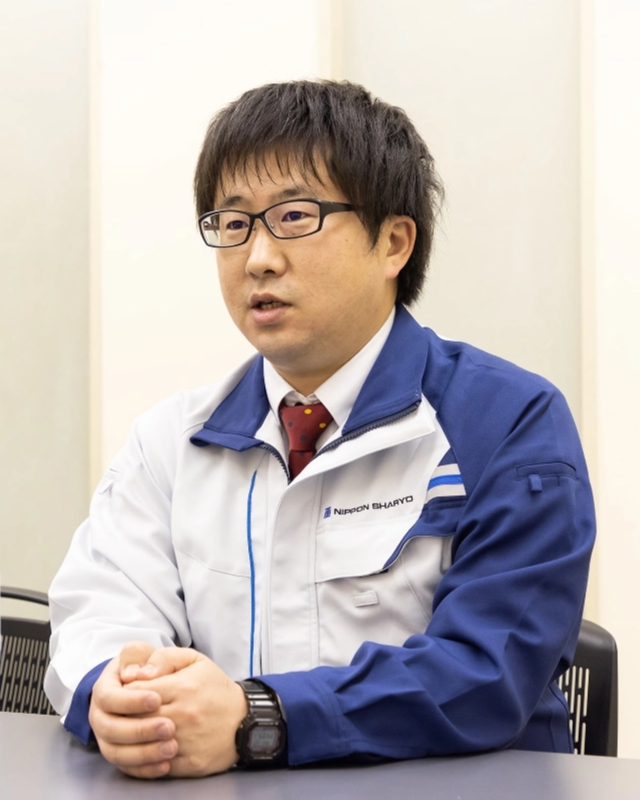
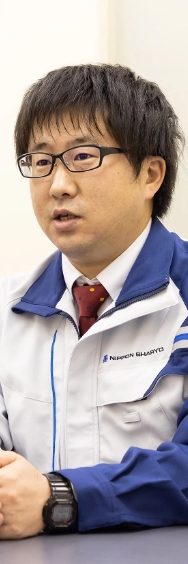
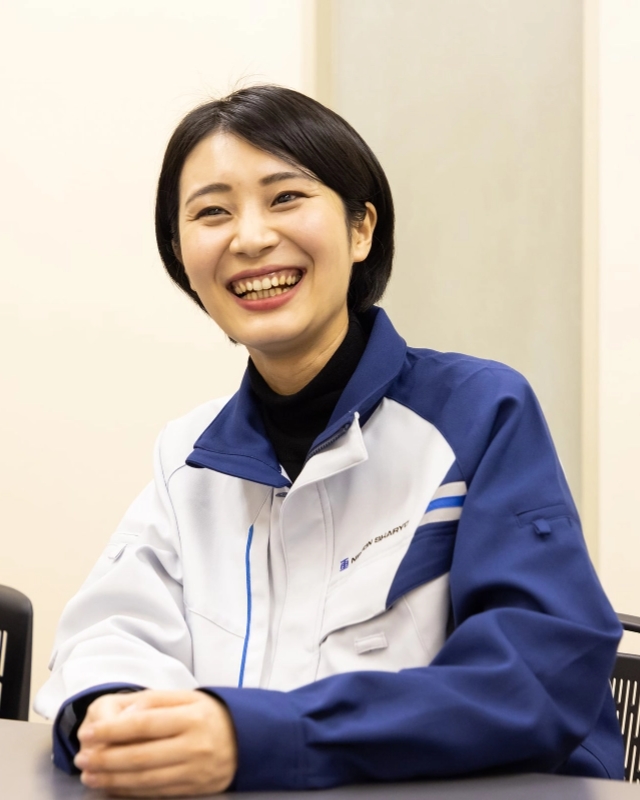
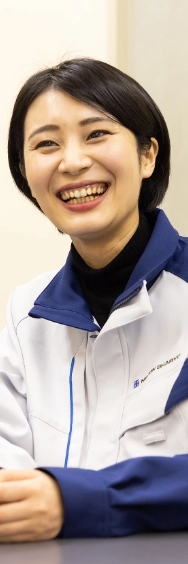
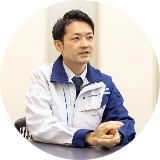
石川
海外営業時代は文化の違いに苦労しました。日本人同士であれば当然理解してもらえるようなこともなかなか理解してもらえないということは日常茶飯事で、お客様の経営陣の交代に振り回されるということも経験しました。難しいプロジェクトでしたが、社内のスタッフはもちろん、現地の取引先などさまざまな人に支えられて乗り切ることができ、自身の視野もとても広がったと思います。仕事は辛いことも大変なこともありますが、すべて成長のチャンスと捉えて、共に苦労し、協力して、前向きに乗り越えていってほしいと思います。
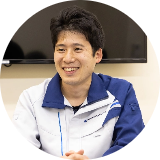
山﨑
私は大学の専攻が材料系で、機械についての知識はほとんどありませんでした。設計に配属され、図面1つ描けない私は、現場やお客様に叩き上げられました。しかし、その知識が今になってとても役立っています。ものづくりの会社ですから図面は苦手とは言っていられません。例え、希望する配属ではなかったとしても、ものづくりの技術や知識はやがて1つに繋がります。どんな部署でもその場で得られるものをしっかりと力にして活躍してほしいと思います。
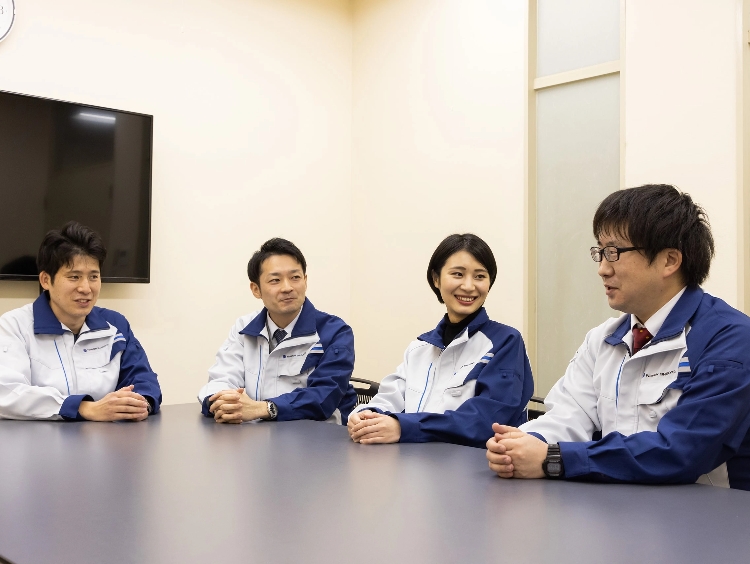