未来をつくる
“最高”を求めてフルモデルチェンジしたN700S。
技術開発を結集した車両には、
日本車両の「最高品質のものづくり」が凝縮されています。
PROJECT MEMBER
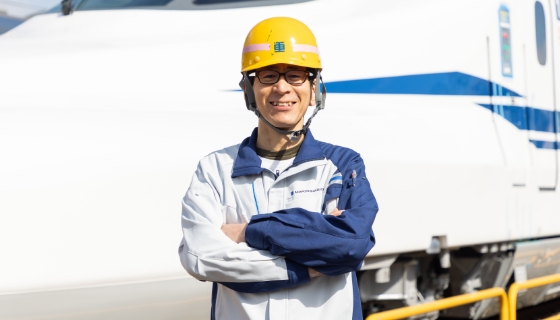
鉄道車両本部
技術部 車体グループ(設計)
1997年入社
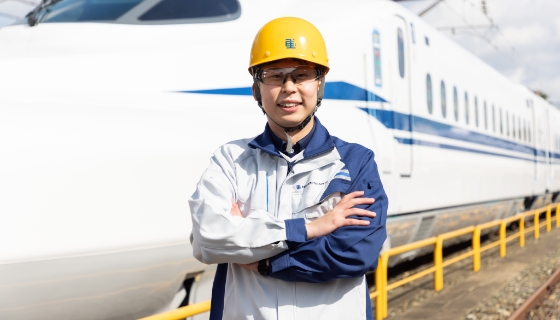
鉄道車両本部
製造部 製造第一課(製造)
2016年入社
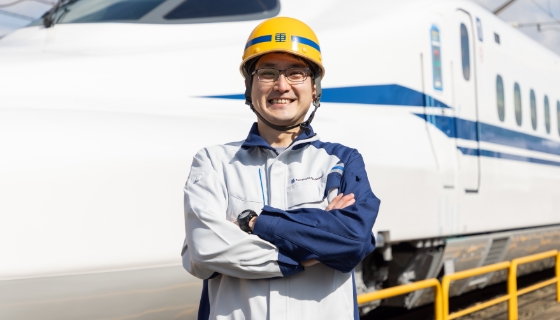
鉄道車両本部
品質保証部 車両検査課 検査三係(品質管理)
2009年入社
※所属・組織名は取材当時のものです
2020年7月1日(水)。東海道・山陽新幹線に新型車両N700Sがデビューしました。
1964年、初めての新幹線が走って以来、
新幹線は日本の大動脈を走る高速鉄道として日本の経済を支えてきました。
N700Sはその最新型車両として、速く快適で、環境にも配慮した技術が凝縮されています。
その開発に関わったのが日本車両のメンバーたち。
大きくメカニズムが変わったと言われる新型車両の開発の裏には
課題解決に奔走した諦めない努力と、大きな成長があります。
標準車両、デュアルスプリームウィング形など、
N700Sの新しいメカニズムとは。
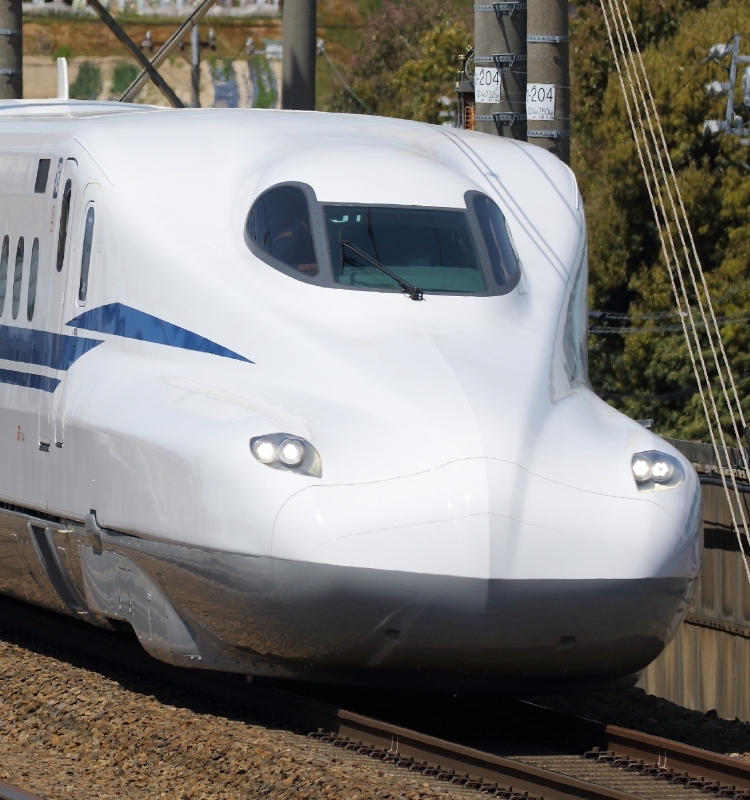
新幹線は、1964年に0系車両がデビューして以来、およそ7〜8年のスパンで新型車両が登場しています。2020年7月にデビューしたN700Sは、2013年に登場したN700A以来、7年ぶりの新型車両となりました。間接照明を採用した車内空間を広く感じる空間デザインや現在地・目的地がひと目でわかる大型ディスプレイの設置、また全席にモバイル用コンセントを搭載するなど、より機能的で快適な空間を実現しています。また、地震発生時にブレーキをかけた際の停止距離を短くするなど、さらなる安全・安定性にも寄与しています。
N700Sはメカニズムを大きく刷新した新開発車両であり、その開発・設計にはさまざまな要件が求められました。
まずこれまでのN700系と大きく異なるのが「標準車両」という構成です。通常、東海道新幹線は16両1編成で運行しています。ところがN700Sは、16両で行われた設計を元に8両、12両と走行区間にあわせ様々な編成の長さに容易に変更できるように構成されています。また従来型よりも空気抵抗や騒音を低減するために、先頭車両の形状には、左右両サイドのエッジをきかせた「デュアルスプリームウィング形」を採用。これにより、省エネルギー効果を高め、環境性能がよりいっそう向上しました。
機器の小型軽量化と機器配置により
「標準車両」という新コンセプトの新幹線が登場。
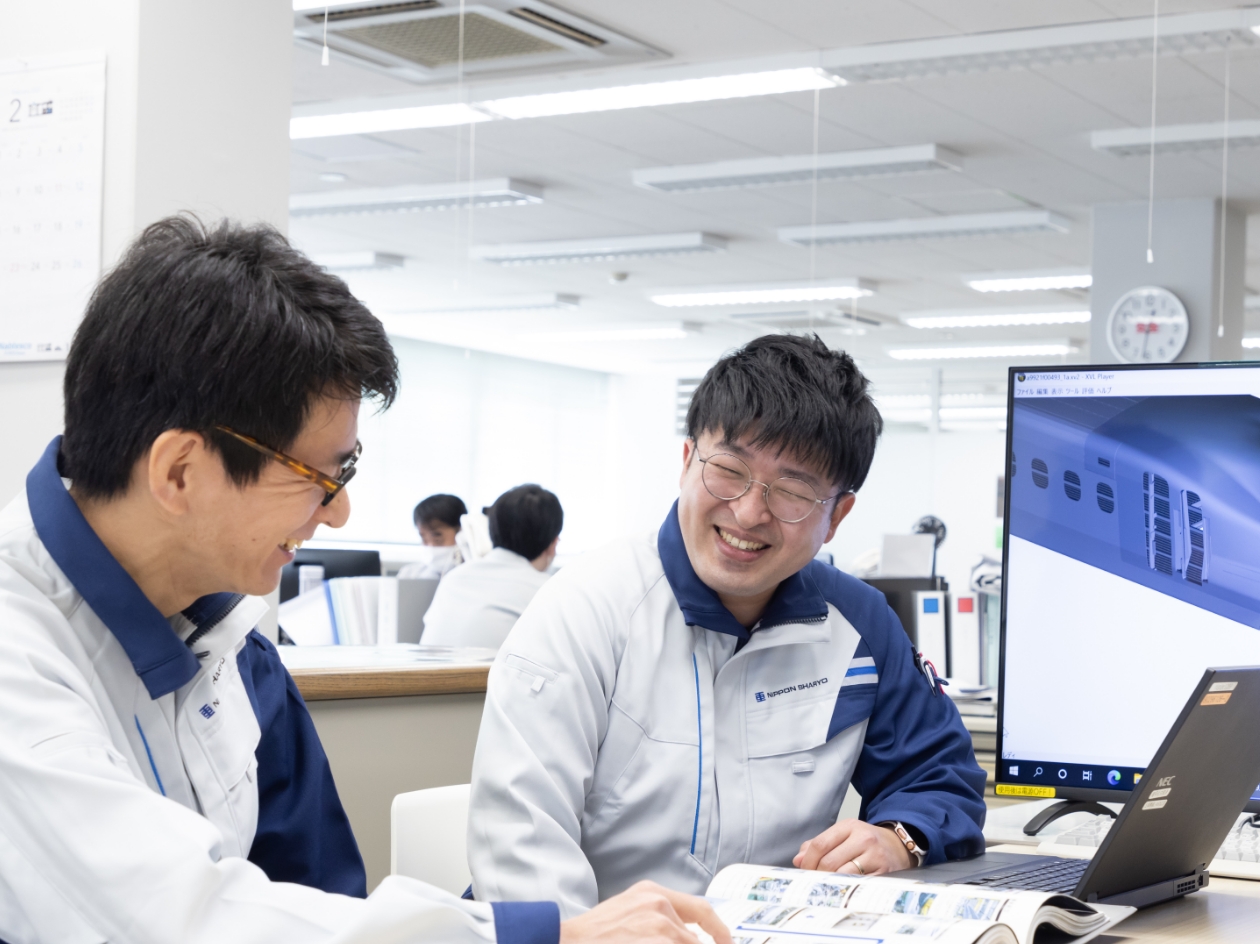
「標準車両」を実現させるために、日本車両が注力すべきは艤装設計でした。設計には大きく分けて車体設計と艤装設計があり、人体に例えるなら、車体設計はプロポーションや肌色、髪型などを理想の姿に整えることを指し、艤装設計は、内臓やそれらを繋ぐ血管や神経をどう配置するかを考えることを指します。具体的には、客室や床下スペースなどの機器配置や、それを動かすための配線、配管を設計するのが主な仕事です。
N700系を含む従来の車両は16両で1編成となっています。主変圧器や主変換装置などを複数車両に分けて搭載するなど、16両だから可能となる機器配置となっていました。それを8両や12両でも編成できる標準編成にするには、今までと全く異なった艤装設計をしなければなりません。しかし、車両の床下スペースや重量には制約があり、N700系のスペースでは収まりきらず、床下機器の小型軽量化と最適な機器配置が課題となりました。
ところが床下機器を製造するのは各種機器メーカーです。各社が最高品質の機器製作を行なったとしても、艤装設計においては、電気配線の場所が100mmズレるだけでも車両設計や製造に大きく影響します。そこで、各機器メーカーとの打ち合わせを繰り返し、設計しやすい機器構成に取り組みました。その際に有効だったのは、早めの情報提供です。例えば「この寸法は50mmに統一してください」など、艤装設計を想定した要望を各メーカーに提案していくことで省スペースでの配置に適した機器が仕上り、またどんな機器になるか予測ができたことで、お客様に対し、早めに図面を提示できました。おかげでお客様との修正のやりとりが格段に減り、詳細な設計に費やす時間が増えたことで、従来は不可能だった機器配置を実現。新しい機器配置により、床下機器の配置種別を8種類から4種類に削減でき、「標準車両」による容易な両数の変更が可能となりました。
より速くより静かに、を求めた先頭車両形状。
製造方法を再検討し、図面通りの美しい形状を実現。
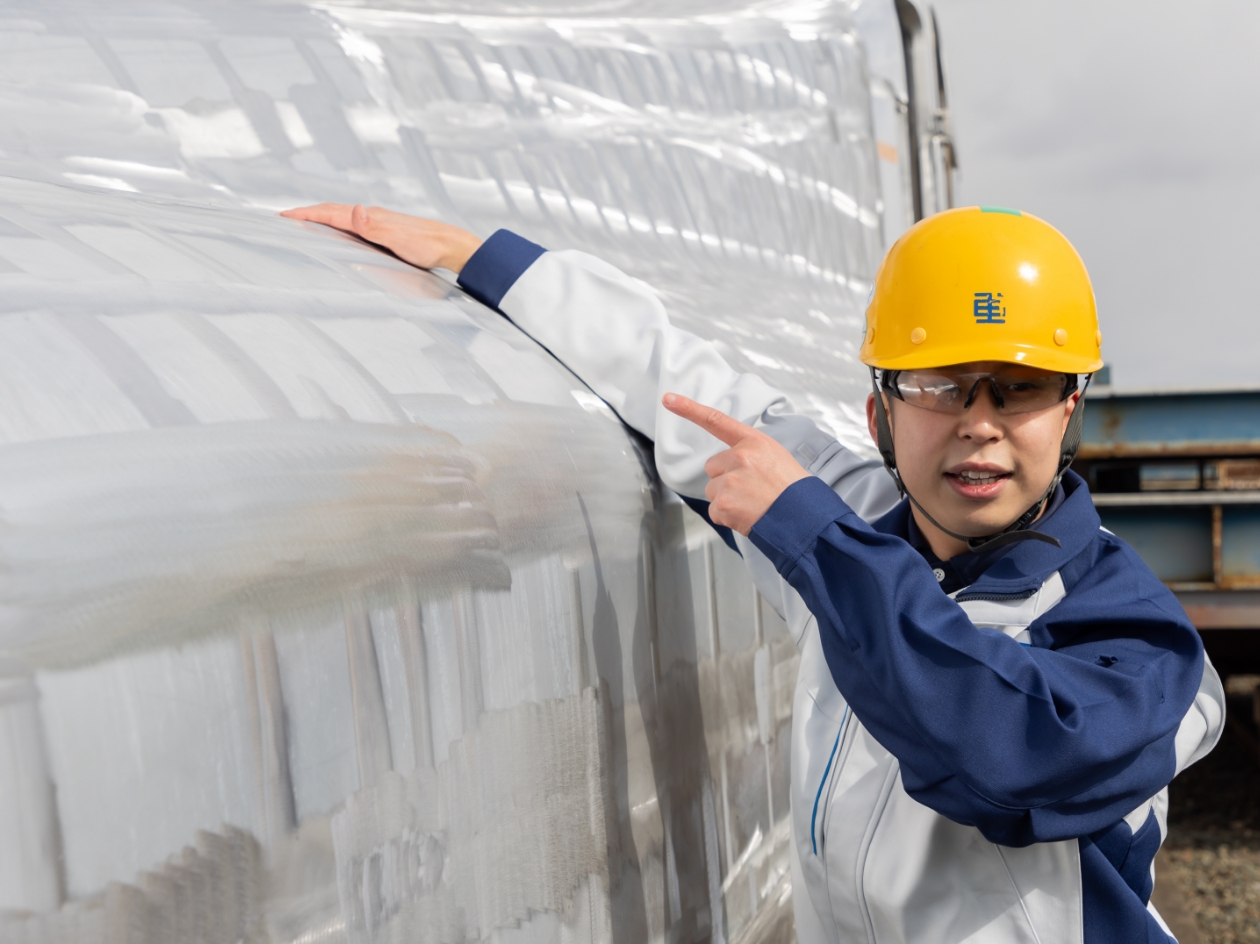
新幹線の高速化は同時に騒音問題をはらんでおり、常に空気との戦いでした。空気抵抗を減らして高速化し、騒音を低減させるため、新幹線の改良では、毎回、先頭車両を流線型でシャープな形状へと変化させてきました。
N700Sで採用されたのは「デュアルスプリームウィング形」です。左右両サイドのエッジが盛り上がったように立っているのが特徴的で、これにより走行抵抗、トンネル微気圧波、騒音、後尾車動揺といった空気性能を向上させ、省エネルギー効果も高まります。
しかし製造においては、エッジの実現が大きな課題になりました。新幹線の顔となる重要な部分ですから、機能的にもデザイン的にも図面通りの実現が求められますが、これまでの製造方法では忠実な実現が難しいと判断したのです。通常、格子状の骨組みの上に外板を取り付けた構造となっており、外板はプレス加工で仕上げています。ところが、「デュアルスプリームウィング形」のエッジの曲線は非常に繊細で、プレス加工で製造するのが難しく、たとえ製造できたとしても骨組みに取り付ける際に、溶接の熱で変形する可能性があります。そこで、現場作業者を交えて、工法を検討。さまざまな検討と検証を繰り返した結果、アルミ板を機械加工で削り出す工法を採用しました。プレス加工よりも重量が増し、コストもかかるため、機械加工を採用するのは「デュアルスプリームウィング形」で強調される部分のみ。結果的にはプレス加工よりも美しいデザインが実現でき、さらに溶接で起こる不具合などの修正作業が減ったことでコストも低減されました。
品質保証は、最高品質を守る最後の砦。
社内外との連携を深めて、スムーズな製造・検査に。
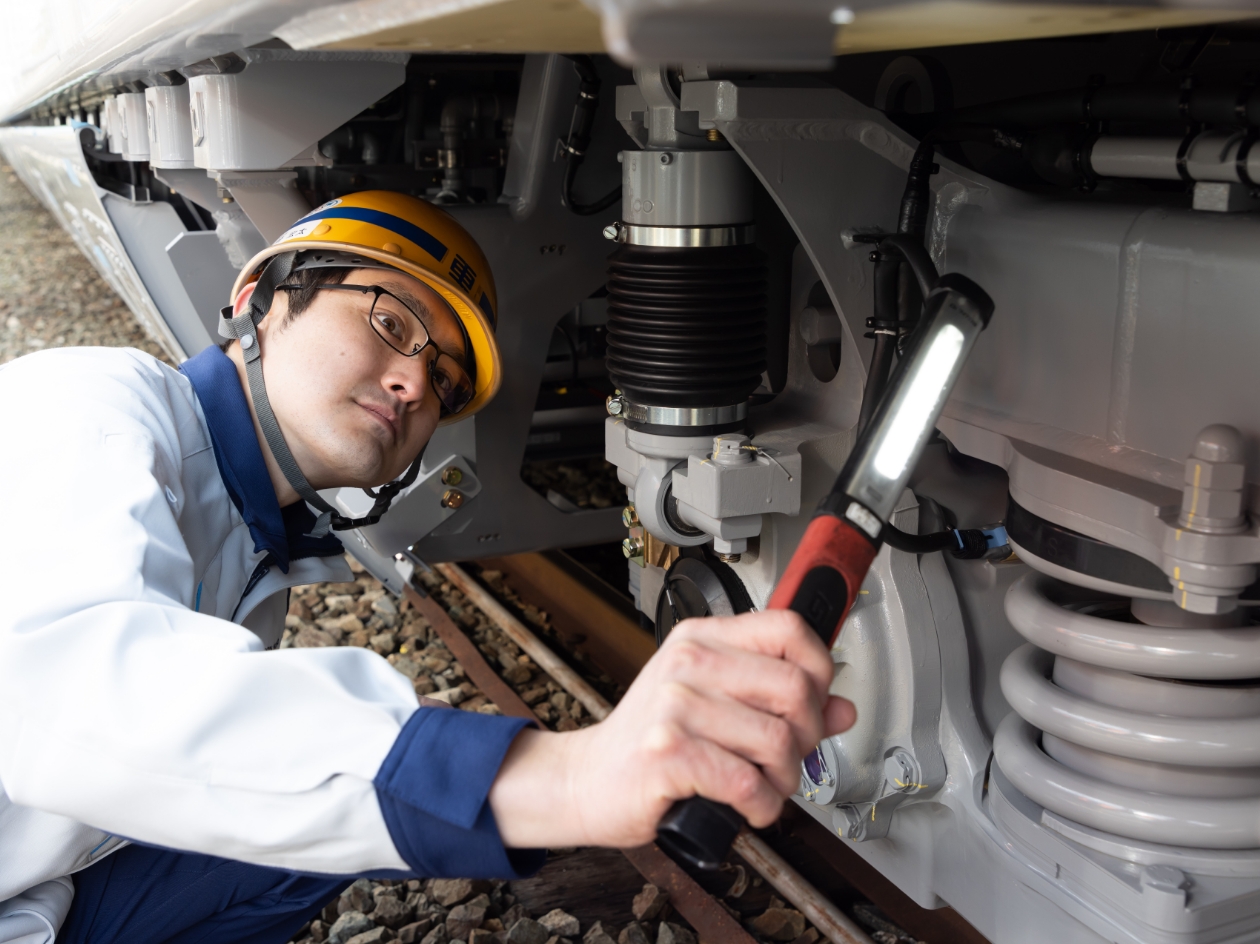
N700AとN700Sを見比べると、外見はあまり変わったように見えませんが、コンセプトやメカニズムが大きく変わり、特に標準車両となったことで新しい機器が数多く搭載されています。検査においては、新しい機器がどんな機能を持ち、どんな不具合が想定されるか、機能発揮や不具合を確認するためにはどんな検査が必要なのか、など、すべてゼロから検証する必要があります。場合によっては、試験装置を新たに開発する必要もあるため、全機器の取扱説明書を取り寄せ、検査の指標となる判断材料を集めていくことがファーストステップとなりました。
車両製作では、N700Aでの経験が活かされました。製造した車両はお客様による最終受け取り確認(完成検査)が実施されますが、その時点でお客様に不合格と判定された場合、手直しに多くの人手がかかり工程に混乱が生じてしまいます。特に内装品の見栄えの検査は判定基準にお客様と社内でギャップがあり、悩まされたことがありました。その教訓を活かし、N700Sでは品質保証部と製造部が情報共有をして判定基準を立案、お客様とも何度も協議、認識合わせを実施することで明確化しました。その結果、両社の想いが詰まった判定基準が確立され、スムーズな製造・検査を実現させることができました。また量産車を製造する前に作られる確認試験車でも大きな課題がありました。量産車は1編成16両が同じ車両メーカーで製造されますが、確認試験車は日本車両と他社の2社で共同製造することになりました。製作所が異なるため、日本車両製作所内試験では、2社が造った車両を連結させて試験することができません。そのため日本車両内で製造した別の車両を通常では行わない号車同士を連結させて走らせなければいけないなど、一筋縄ではいきませんでした。また検査には初期トラブルがつきものです。製作に関わる2社で情報共有し、工程を守りながら不具合のない車両を作り上げていくことには苦労しました。
最後のJR東海敷地内での試験では陣頭指揮を任され、無事にテスト走行した時は、お客様に「よくやってくれました」とお褒めの言葉をいただき、慰労の懇親会を開いてくださいました。現在も大きなトラブルなく走行していることが、私たちの一番の達成感です。
一人の力を結集させて信頼を守り、
最高品質のものづくりを実現させていく。
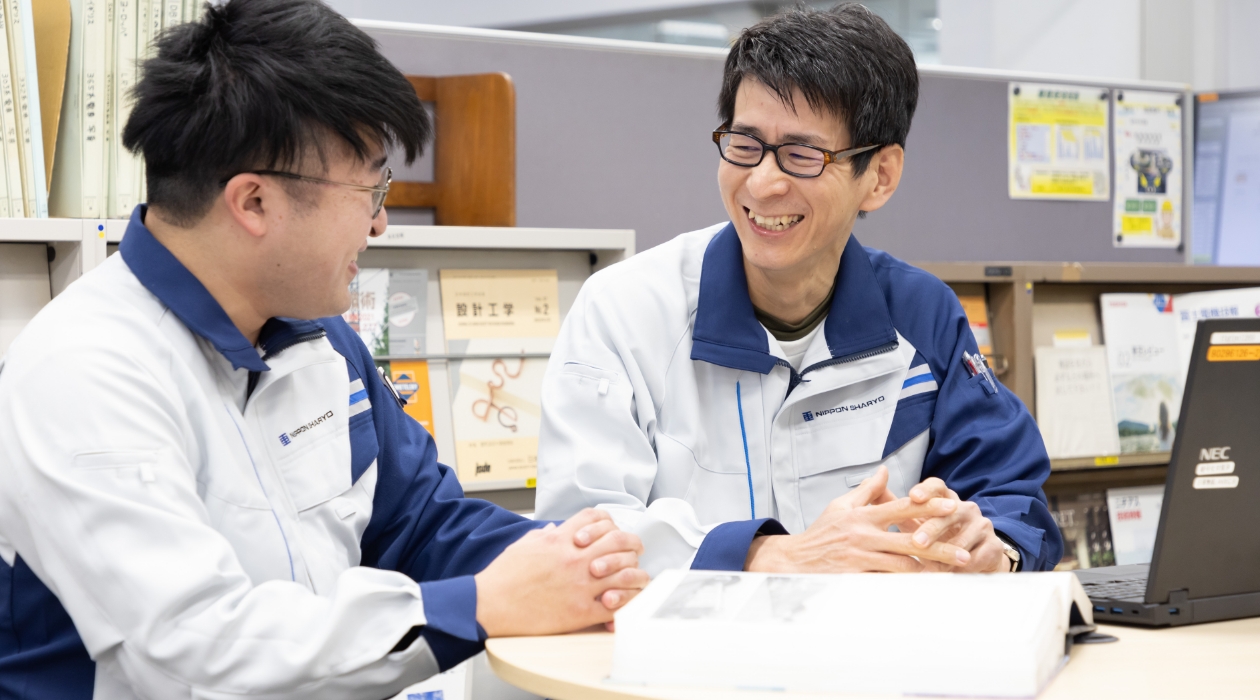
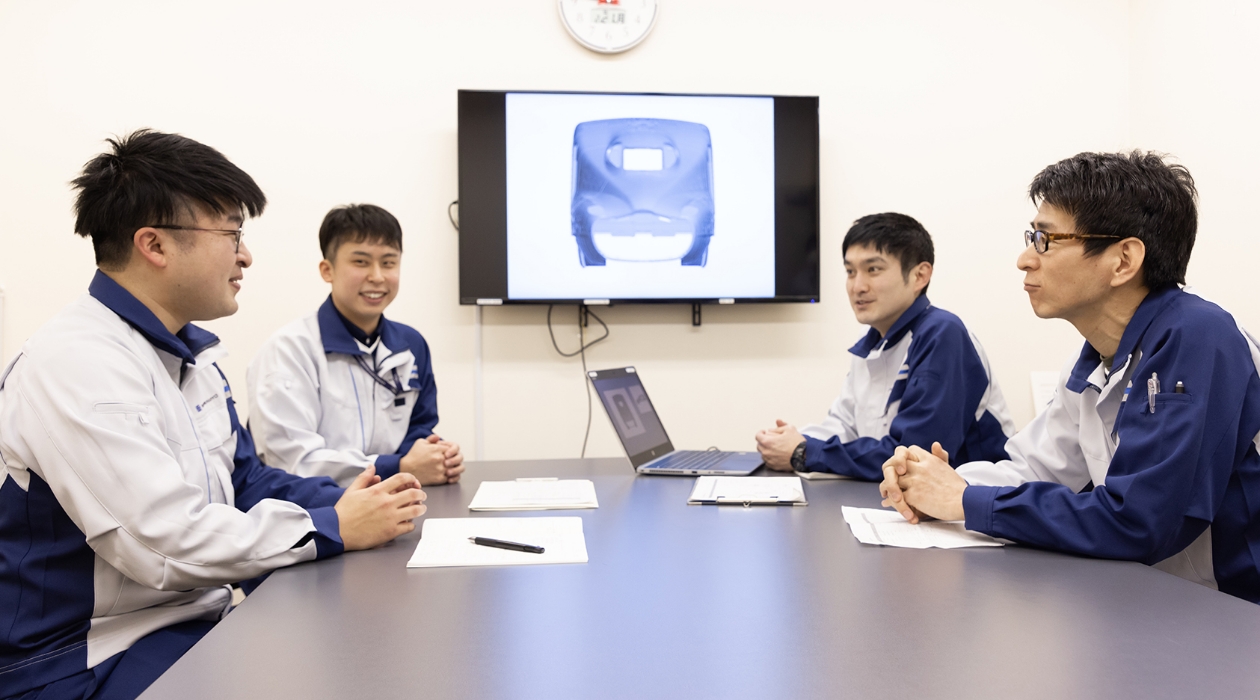
N700Sの開発プロジェクトがスタートしたのは2013年。前型のN700Aがデビューしたのが2013年ですから、新車両が登場するや否や、次世代の車両開発が始まっていることがわかります。最初は客室の技術開発からはじまり、製作性の向上や省エネルギーへの配慮がテーマとなりました。
お客様であるJR東海との打ち合わせにより仕様が固まる中、日本車両の社内では製作性の向上にどう取り組むかが課題となっていました。1つの部署で解決できる問題ではないため、設計から資材・製造・検査の部署間を横断したメンバーが1つのプロジェクトチームとなり、全体でミッションを解決していく体制を取ることになりました。検査の許容範囲はどのくらいか、それを守るためにはどのように製造したらいいのか、基準内に製造するにはどのような設計がいいのか、など、設計から製造、検査へと流れるものづくりの工程を逆算して、よりよいものづくりを検討したのです。こうしたN700Sの開発のあり方がベースとなり、各部署の連携を深める体制が社内にて本格化されました。
この体制により、社内外とのコミュニケーションが重要となり、メンバーの情報収集や発信力、納期や品質を守る責任感、他部署のことにも自ら関わる主体性などが高まったと思います。中には現場の指揮を任され、リーダーとしてのスキルを高めたメンバーも多くいました。
新幹線に限らず、日本車両のものづくりは安全安心が当たり前の世界。N700Sは安全安心かつ快適に走行することを約束している乗り物です。その約束を守り抜くことが日本車両の最高品質のものづくりです。
1人の力を部署の力に、部署の力を会社の力に集結していき、「品質の日車」「納期の日車」と呼ばれる私たちの信頼に結んでいき、これからも一人ひとりみんなの力を合わせて最高品質のものづくりに挑み続けます。
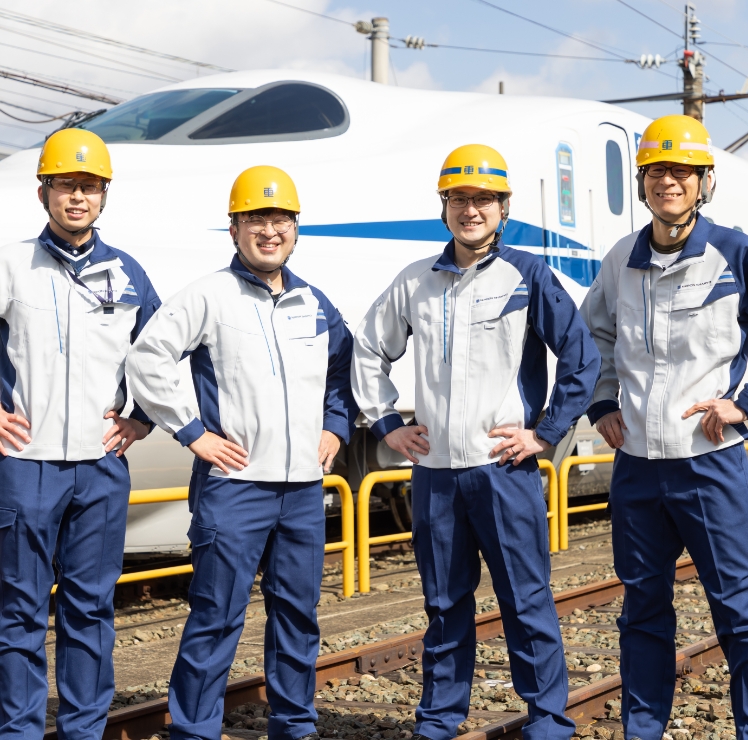